drivetrain losses: introduction
Drivetrain losses are an important factor in cycling. A sort of canonical number is they are responsible for 3% of total power during high-intensity riding. Wilson's Bicycling Science 3rd edition (2004, MIT Press) page 343 shows data indicating at 200 watts, losses vary from 2.4% to 3.1% among three gear choices with a clean chain:
A comparison of a "no rust, lubricated" chain to a "rusty, dry" chain yields a difference of 4-5% (absolute) at 200 watts, which is huge.
Anyway, from these data it's clear a fixed "drivetrain efficiency" is a poor model. Even if you allow the efficiency to vary from one gear to another, there's a clear power dependence. And allowing an "efficiency" to vary with power is obviously obfuscated: you're applying a model that drivetrain losses are proportional to total power but then allowing that proportionality constant to vary with power. Better to use a proper model.
Spicer, in Human Power (2000) did some very nice measurements using motors, which allowed him to set the cadence, gear, and power independently. Thus he was able to measure drivetrain efficiency at the same chain speed and tension for different rear cogs.
Spicer's efficiency measurements as a function of reciprocal chain tension for each of three rear cogs
These were his conclusions:
It was found that larger sprockets provide more efficient transfer of power while smaller sprockets proved to be less efficient. Simple, frictional loss models were developed that gave sprocket-size loss variations that agreed with those variations measured experimentally. Typically, a 2–5% loss difference was measured between the 52–11 and the 52–21 sprocket combinations depending on the drive operating conditions.
Experimental results indicated that the efficiency of the chain drive varied as a function of chain tension. It was found that the efficiency varied linearly with the reciprocal of the average chain tension with the highest efficiencies occurring at high chain tensions and lowest at low chain tensions.
It was found that chain-line offset and chain lubrication have a negligible effect on efficiency under laboratory conditions.
A follow-up article by Walton and Walton (a high school senior and her college professor father) reanalyzed Spicer's data for the case where power and speed were fixed, but cadence was allowed to vary. This more accurately represents the case where a rider is trying to choose in which gear to ride on a given section of roadway.
But there's another case to consider, which is whether it's more efficient to ride with a 110 mm BCD "compact" crank (for example, a 36/24) or the equivalent gear with a 130 mm BCD "conventional" (for example, a 39/26). Is one more efficient than the other? This question has been discussed in online forums, but I can't say I've seen a clear conclusion on the matter.
Personally, I find Spicer's claim efficiency is higher at higher chain tension to be puzzling. All other things equal, how can increasing the chain tension reduce the power loss in the chain? It makes no sense. We were all taught in high school physics that frictional force between two surfaces is proportional to the normal force between those surfaces. If the chain tension increases, the links and pins of the chain should be pressed harder together, and drivetrain losses should increase, not decrease as Spicer suggests. Yet the measurements are real.
The issue is that chain tension is not an independent variable. Power delivered by the chain equals the product of the chain tension times the chain speed: that's simple physics. So if chain speed is fixed, and tension is increased, then power is increased. Instead of pursuing this further, and getting confused, I'll propose my own model for drivetrain losses, then compare the results with Spicer's data.
Frank Berto and Chester Kyle's data.
Then in Human Power 52 (2001), Frank Berto and Chester Kyle did some nice measurements comparing a geared drivetrain (a Shimano Ultegra mountain bike group (?), 22,32,44 by 12,14,16,18,20,23,26,30,34) with various internal geared hubs. The advantage over the Spicer data was that more gear combinations were tested, although each gear combination was tested less extensively.
I'll propose a simple model next time.
A comparison of a "no rust, lubricated" chain to a "rusty, dry" chain yields a difference of 4-5% (absolute) at 200 watts, which is huge.
Anyway, from these data it's clear a fixed "drivetrain efficiency" is a poor model. Even if you allow the efficiency to vary from one gear to another, there's a clear power dependence. And allowing an "efficiency" to vary with power is obviously obfuscated: you're applying a model that drivetrain losses are proportional to total power but then allowing that proportionality constant to vary with power. Better to use a proper model.
Spicer, in Human Power (2000) did some very nice measurements using motors, which allowed him to set the cadence, gear, and power independently. Thus he was able to measure drivetrain efficiency at the same chain speed and tension for different rear cogs.

These were his conclusions:
It was found that larger sprockets provide more efficient transfer of power while smaller sprockets proved to be less efficient. Simple, frictional loss models were developed that gave sprocket-size loss variations that agreed with those variations measured experimentally. Typically, a 2–5% loss difference was measured between the 52–11 and the 52–21 sprocket combinations depending on the drive operating conditions.
Experimental results indicated that the efficiency of the chain drive varied as a function of chain tension. It was found that the efficiency varied linearly with the reciprocal of the average chain tension with the highest efficiencies occurring at high chain tensions and lowest at low chain tensions.
It was found that chain-line offset and chain lubrication have a negligible effect on efficiency under laboratory conditions.
A follow-up article by Walton and Walton (a high school senior and her college professor father) reanalyzed Spicer's data for the case where power and speed were fixed, but cadence was allowed to vary. This more accurately represents the case where a rider is trying to choose in which gear to ride on a given section of roadway.
But there's another case to consider, which is whether it's more efficient to ride with a 110 mm BCD "compact" crank (for example, a 36/24) or the equivalent gear with a 130 mm BCD "conventional" (for example, a 39/26). Is one more efficient than the other? This question has been discussed in online forums, but I can't say I've seen a clear conclusion on the matter.
Personally, I find Spicer's claim efficiency is higher at higher chain tension to be puzzling. All other things equal, how can increasing the chain tension reduce the power loss in the chain? It makes no sense. We were all taught in high school physics that frictional force between two surfaces is proportional to the normal force between those surfaces. If the chain tension increases, the links and pins of the chain should be pressed harder together, and drivetrain losses should increase, not decrease as Spicer suggests. Yet the measurements are real.
The issue is that chain tension is not an independent variable. Power delivered by the chain equals the product of the chain tension times the chain speed: that's simple physics. So if chain speed is fixed, and tension is increased, then power is increased. Instead of pursuing this further, and getting confused, I'll propose my own model for drivetrain losses, then compare the results with Spicer's data.
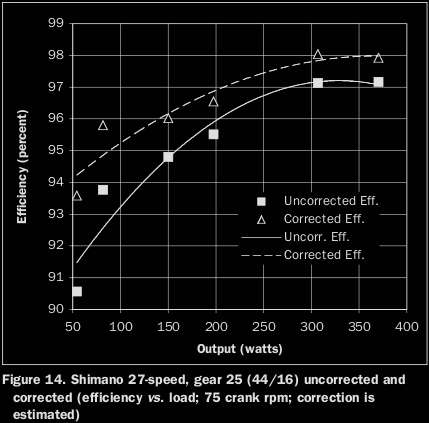
Then in Human Power 52 (2001), Frank Berto and Chester Kyle did some nice measurements comparing a geared drivetrain (a Shimano Ultegra mountain bike group (?), 22,32,44 by 12,14,16,18,20,23,26,30,34) with various internal geared hubs. The advantage over the Spicer data was that more gear combinations were tested, although each gear combination was tested less extensively.
I'll propose a simple model next time.
Comments
An alternate thought is related to the accuracy of the measurement equipment. Not knowing how accurately the tester was able to measure the input and output power, it could simply be that we are seeing the absolute values of a fixed error on an increasing input and output. As of the last few years there are some sophisticated load testers the can detect very small (<<1W) differences in load; whether this equipment existed at the time these data were gathered, and whether it was used in the test, is unknown.